Bottle caps
Bottle caps are used for closing or sealing the top opening of a bottle. They are designed to contain the product inside the container without external leaks and ensure that the quality of the product is maintained. Some bottle caps are designed to dispense liquid products like condiments, oils, sauces, etc. They find wide use in food and beverage, FMCG, pharmaceutical and chemical industries.
Types of bottle caps
There are multiple types of plastic bottle caps based on their design. The caps are designed to work with different types of liquids of varying viscosities. It can be a simple screw cap that enables the consumer to pour directly from the bottle to release a specific volume of product through the cap hole fitted with a silicon release valve. There are various models of bottle caps like screw cap, disc top cap, flip top cap, bottle over the cap, twist top cap, push/pull cap, nozzle pull top cap, double button disc top cap, double-twisting locking cap for pharmaceutical products, dosing bottle cap, etc. and custom made to fit each application. The metal caps of bottles are usually crown cork type or threaded type. The jar lids are mostly of lug cap type. Plastic bottle caps are generally used on plastic bottles and metal caps on glass bottles. Some metal caps have a plastic coating on them. The caps may also have brand information printed on them.
Ideal characteristics of bottle caps
The following are the ideal characteristics of a bottle cap. It should have good:
1) Mechanical properties like strength and toughness, elasticity/ flexibility to withstand forces of pressure/impact and durability;
2) Insulation properties like firm sealing and leakproof, resistance to moisture, water vapor, gas, light, odor and heat;
3) Safety characteristics like non-toxicity, corrosion resistance, insect/pest-proof and anti-microbial property,
4) Processing features like suitability to be processed into various products and feasibility for use in automated operations, its suitability for printing, etc.;
5) Other reasons like a wide range of sources, easy availability, low cost, and ease of handling the raw materials.
Materials used for making bottle caps
Bottle caps are mostly made of plastics. They may also be made of metal. The material for the manufacture of bottle caps is chosen based on its usage and type of bottle/container. The properties like strength, flexibility, durability, inertness to liquid compositions and moisture resistance are considered carefully before being chosen for an application.
- Plastics
The plastic caps are usually made of Polyethylene Terephthalate, Polypropylene, Low-Density Polyethylene, High-Density Polyethylene, Polyvinyl Chloride, Polystyrene and Polycarbonate.
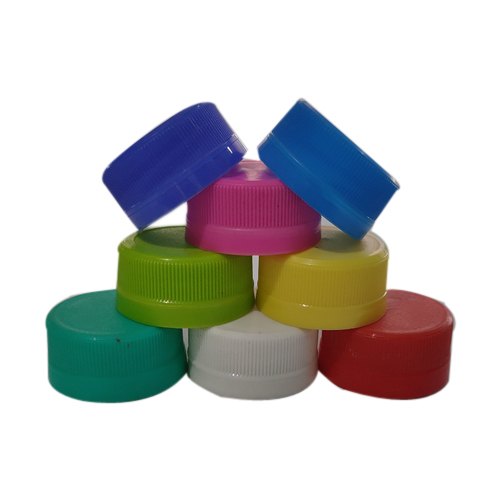
Polyethylene Terephthalate (PET) is non-toxic, light in weight, strong and durable, environmentally friendly and recyclable. It is used in plastic bottles that package carbonated beverages, mineral water, dairy beverages, juices, edible oil, etc.
Polypropylene is non–toxic, high plastic, environmentally friendly, recyclable, and degradable. It has good barrier properties and is resistant to chemicals. It is used in heat-resistant beverage bottles, edible oil packaging bottles and other plastic food packaging containers.
Polyethylene is of two types, LDPE (Low-Density Polyethylene) and HDPE (High-Density Polyethylene). It has stable chemical properties, good acid resistance, good alkali resistance, high barrier properties and good sealing performance. It has low heat resistance. It is used in chemical plastic packaging, plastic test tubes and in health product packaging bottles.
Polyvinyl Chloride is a thermoplastic material that is used in rigid and flexible forms. It is transparent, light and highly durable.
Polystyrene is a rigid, strong, transparent resin polymer. It has reasonable moisture absorption characteristics and chemical resistance. It is used for making small jars, bottle caps, cups and storage containers.
Polycarbonate is a thermoplastic polymer that is strong and transparent and used in the manufacture of food and beverage storage containers.
Polyethylene naphthalate is a new type of polyester packaging material with good gas barrier properties, Ultraviolet light and heat resistance.
2. Metals
The metal caps are usually made of steel and aluminum. They have a wide range of temperature tolerance and are resistant to fracture from impact. The steel caps are usually coated with an anti-corrosive coating of chrome plate or tin plate. Other materials like plastisol, pulp/aluminum Foil, or solid PE (polyethylene) are also used.
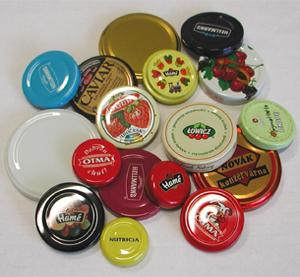
3. Liners
These coatings applied on the caps are referred to as liners. The liners are chosen based on the product’s nature and may specifically be used for moisture barrier, chemical resistance, safety, or prevention of leakage. The different types of liners are 3-ply foam, polyethylene foam, pressure-sensitive foam liner, induction liner, polyvinyl, poly seal, Teflon PTFE, foil and plastisol.
3-Ply foam liner is made of compressible polyethylene foam with a layer of polyethylene film. They have excellent sealing characteristics, good chemical resistance, good taste and odour resistance and low water vapour transmission rate. They form a compressible seal and are mostly used for the prevention of leakage and are ideal for packaging non-acidic foods.
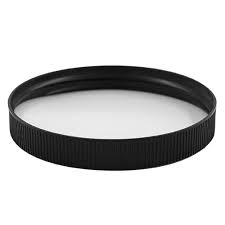
Polyethylene foam liner is also made of compressible foam and lined with LDPE and is used to prevent leakage.
HDPE Foam liners are acid resistant, where the LDPE core is sandwiched between layers of virgin HDPE.
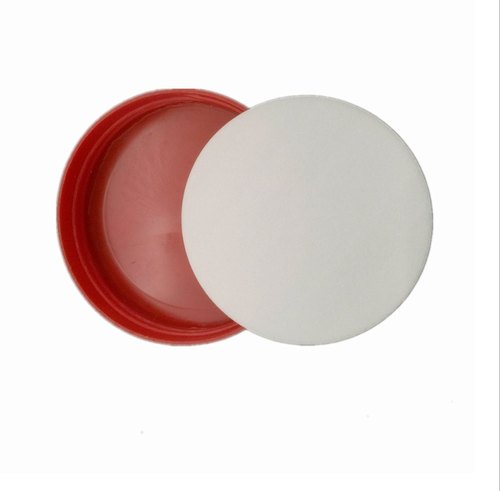
Pressure Sensitive foam liner has an adhesive side that sticks to the container with the pressure used, to stick onto the rim of the container. When the cap is removed, the pressure-sensitive liner remains on the top of the container.
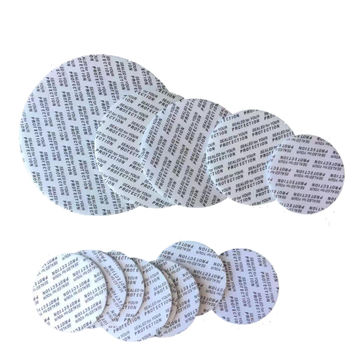
The induction liner is made with layers of pulpboard, wax, foil and polymer coating. The liners are applied to the container with the use of an induction sealing machine. When the liner is heated, the wax melts into the container creating an airtight, hermetic seal.
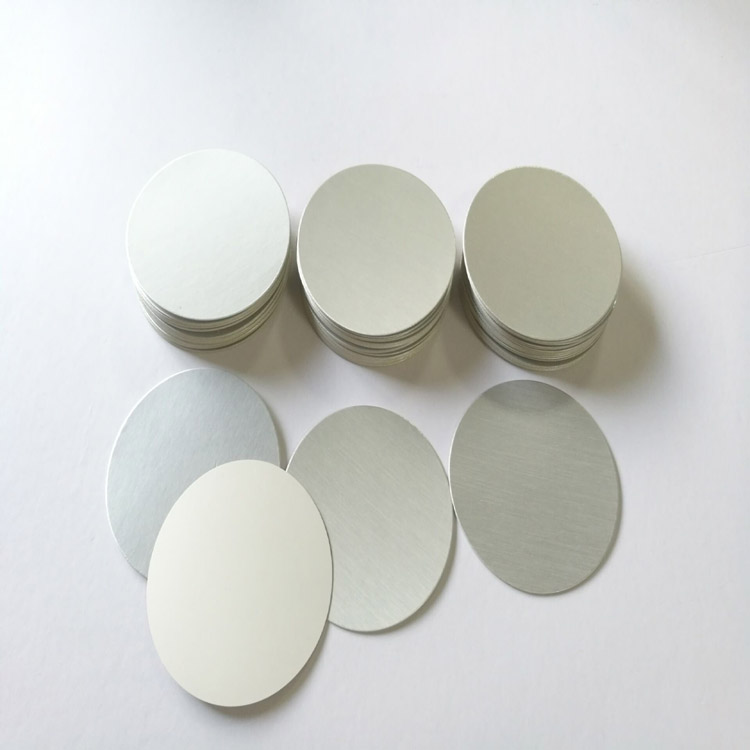
The poly seal is an LDPE cone liner that creates a wedge type seal across the top of the container providing a leak-proof seal for liquid products, virtually eliminating leakage, evaporation and contamination. They form an exceptionally tight seal and offer a good chemical barrier. They are good for use with acid products and essential oils.
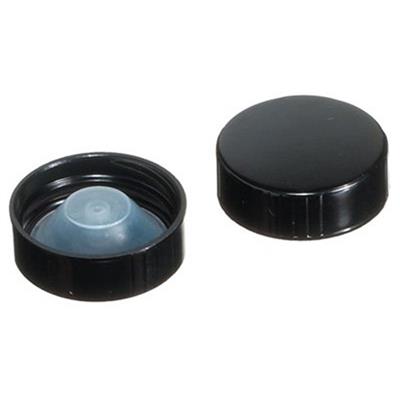
Teflon PTFE (Teflon Polytetrafluoroethylene) has a silicon/rubber core with a Teflon lining facing the product. It has good sealing and chemical resistance properties.
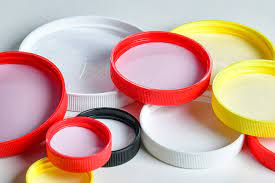
Foil liner is made of paper pulpboard that is bonded to a polyester film laminated to aluminum foil. It can be used for non-acid and non-alkaline products. There are also tin-foil liners available.
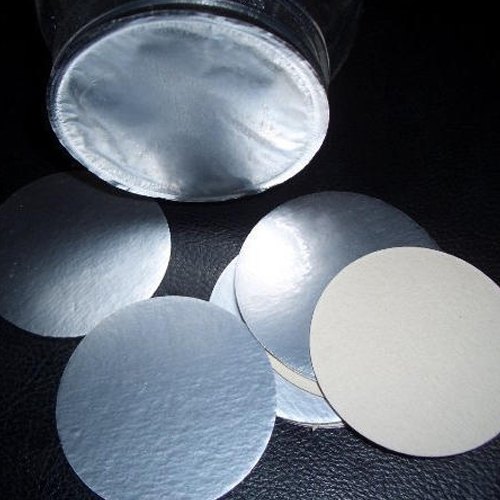
Plastisol liner is a standard lining material that is used in metal closures for vacuum packing glass bottles and jars. It is a plastic gasket that lines a metal cap and creates an airtight seal during “hot-fill” operations. This liner is effective only when the temperature of the bottle is at 140 degrees F when applied, to cause the liner to soften and form a hermetic seal around glass containers. It is a flowed-in compound, usually a dispersion of PVC resins in plasticizers. It is highly resistant to mild acids.
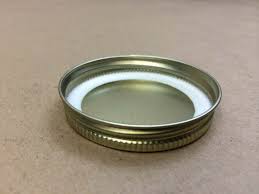
Gaskets are used in the lids for an air-tight seal. It has to be made sure that the gasket of the cap is in place during the sealing operation when pressure is applied to the cap. Also, suitable gasket material, usually rubber or plastic, should be chosen considering the chances of air/ water leak during the displacement of seal joint of gasket due to shrinkage or expansion of bottle cap in conditions of heat and impact. The gasket material may be incorporated with oxygen absorbing substances, that absorb the infiltrated oxygen from the neck part of the bottle and helps keep the product fresh.
National and International regulations on the migration limits of food contact packaging materials
In India, the Food Safety and Standards (Packaging Regulation), 2018 under the FSS Act, 2006 gives details on the specific migration limits of substances from plastic materials intended to be in contact with articles of food, the list of standards for the food contact plastic materials and suggestive packaging materials.
In Canada, all packaging materials used in the sale of foods are subject to the provisions of Division 23 of the Food and Drug Regulations. The manufacturers voluntarily submit the packaging material to the Health Protection Branch of the Food Directorate’s Bureau of Chemical Safety, which conducts evaluations on the chemical safety of products and issues a No Objection Letter if the product is acceptable for the specified food packaging end-use.
In the USA, the Title 21 Code of Federal Regulations of the US FDA lists the regulatory specifications for Food Contact Materials. It provides details on the Indirect Food Additives, which are generally the adhesives and components of coating, polymers, etc, its specification, conditions of use, extraction limitations, etc.
In Europe, the EU legislation on specific materials includes the EU Commission Regulation (EU) No.10/2011 on plastic materials and articles intended to come into contact with food. It establishes the specific requirement for the manufacture and marketing of plastic materials and articles and its specific migration limits (SML) and Overall migration limits.
In Australia and New Zealand, manufacturers are required by the Food Standards Code to ensure food in contact with packaging is safe. The Australia New Zealand Food Standards Code – Standard 1.4.1 – Contaminants and Natural Toxicants sets out the maximum levels of some contaminants that may be present in food as a result of contact with packaging material. The Australian Standard – Plastics materials for food contact use (AS 2070-1999) details on the plastic materials and colorants for food contact use.
In Japan, the Japan External Trade Organization has published Specifications and standards for Foods, Food additives, etc. under the Food Sanitation Act. which includes the standards on materials that contact with food.
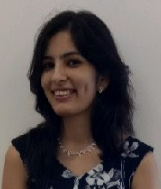