Introduction to Heat Exchanger
A heat exchanger is a device, which transfers thermal energy between two fluids at different temperatures. In most thermal engineering applications, both the fluids are in motion and the main mode of heat transfer is convection. Examples are automobile radiators, condenser coils in the refrigerator, air conditioners, solar water heaters, chemical industries, domestic boilers, oil coolers in a heat engine, and milk chillers in pasteurizing plants.
Classification according to construction:
- Plate Type Heat exchangers
- Shell and Tube heat exchanger
- Scraped surface heat exchanger
Plate-type heat exchanger
A plate heat exchanger is used to transfer heat energy from one fluid to another. These fluids never encounter each other due to being separated by the heat exchanger. Typically, a plate heat exchanger will consist of several parallel plates positioned above each other, thus creating a passage in which the fluid can flow between.
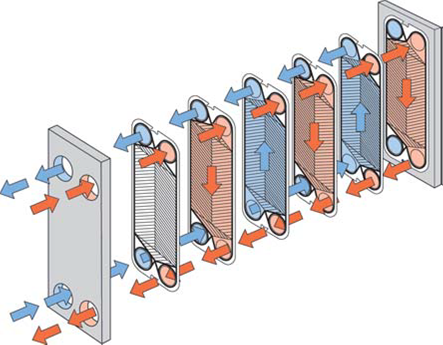
Working Principle
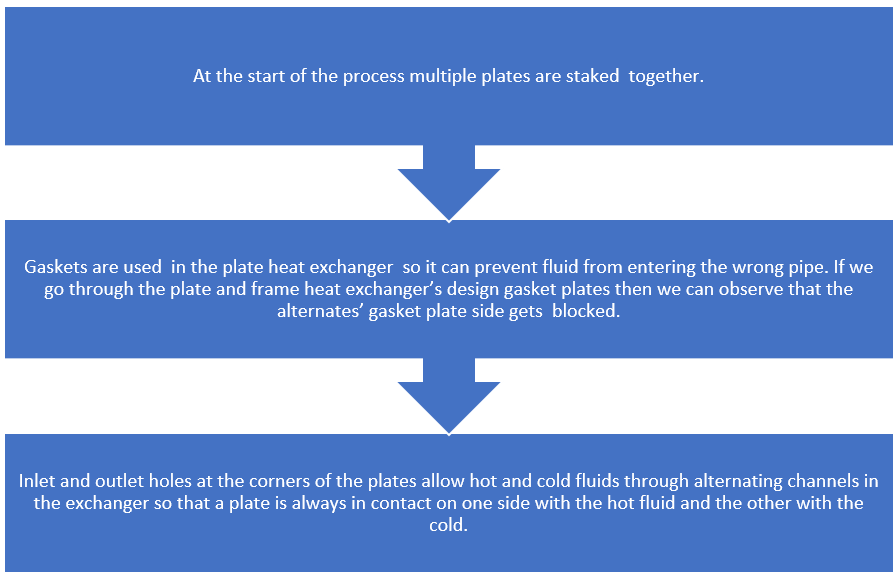
Shell and tube type heat exchanger
The shell and tube heat exchanger consists of a bundle of round tubes placed inside the cylindrical shell. Shell and tube heat exchangers transfer heat between a bundle of tubes surrounded by a large shell vessel. Tubes enable the processing of fluids that are more viscous or contain more particulate or larger matter. Fluids that run through the tubes exchange heat with fluids that run over the tubes contained by the shell. The baffles provide support to tubes and deflect the fluid flow normal to tubes.
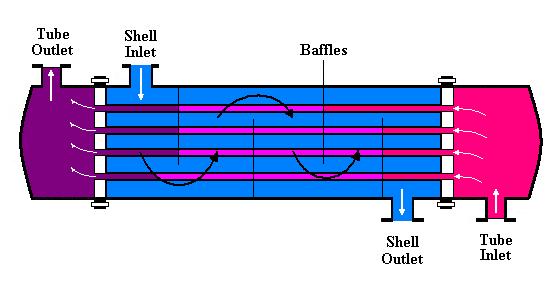
Working Principle
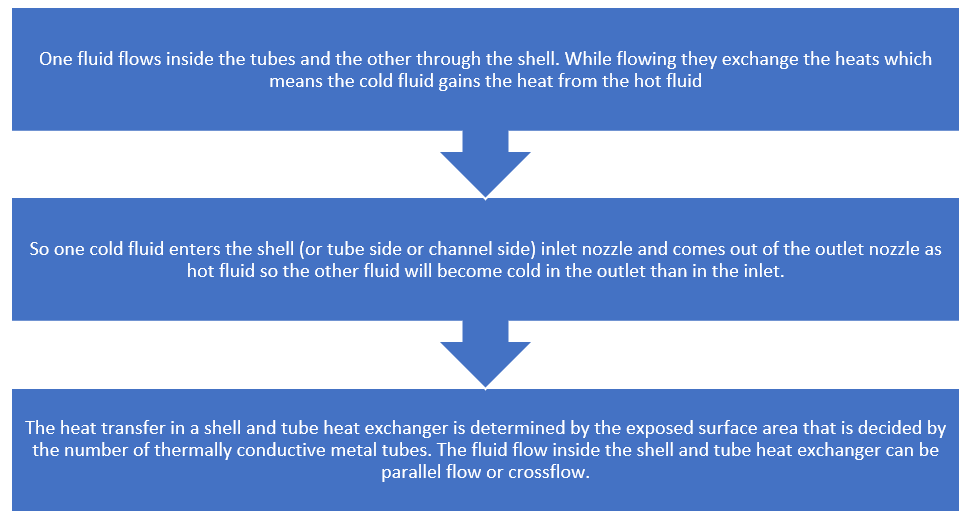
Scraped Surface Heat exchangers
Some processes require heat transfer that prevents fouling from viscous and sticky products. In those processes, scraped surface heat exchangers are the right choice because of their ability to process fluids that include a high number of particulates or high viscosity. Scraped surface heat exchangers are often more expensive than other exchangers but work more efficiently in applications where other options would be ineffective.
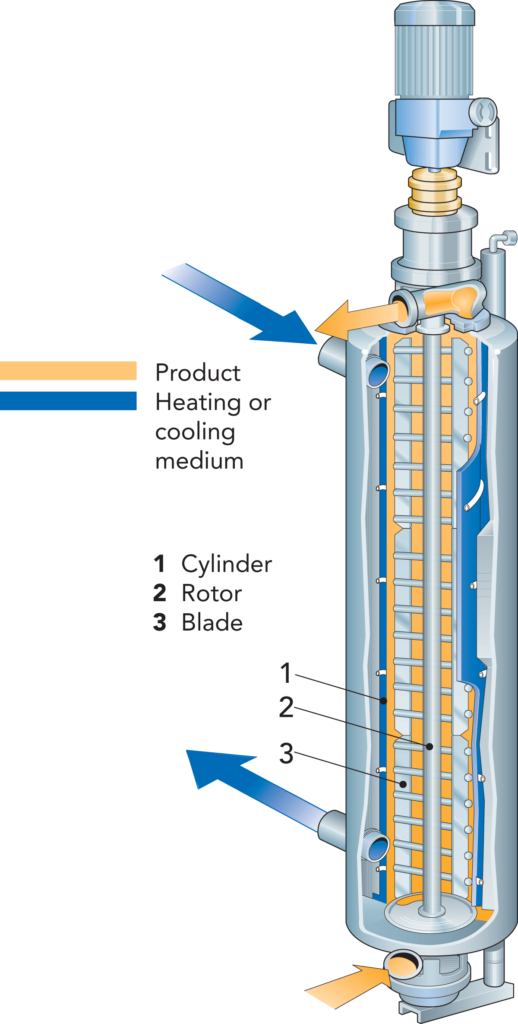
Working principle
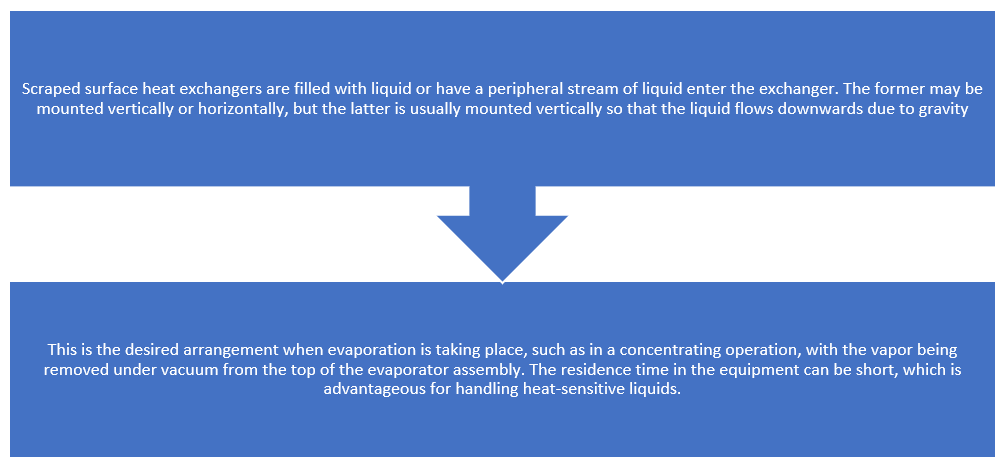
Comparison between plate heat exchanger, Shell and tube exchanger, and scraped surface exchanger
Characteristics | Plate Heat Exchanger | Shell and Tube Exchanger | Scraped surface Exchanger |
Cost | Inexpensive compared with other designs | Inexpensive compared with other designs | Relatively more expensive than other designs |
Cleaning | Excellent CIP-ability | Excellent CIP-ability | CIP-ability is lower than in other designs |
Heat regeneration | High heat regeneration | Medium heat regeneration | No heat regeneration |
Capacity | Easy to increase/decrease capacity | Difficult to expand capacity | Difficult to expand capacity |
Footprint | Smaller footprint than other designs | Larger footprint than plate-and-frame designs | Smaller footprint than other designs |
Pressure | Low operating pressure | High operating pressure | High operating pressure |
Fluidity | Not for use with highly viscous or large particulate fluid | Not for use with highly viscous products or products with large particulates | Highly effective with viscous products or products with large particulate fluids |
Pressure | High Turbulence | Medium operating pressure | None |
Applications | Plate heat exchangers are commonly used for beverage, beer, wort, eggs, sauces, and most dairy processing | Shell and Tube heat exchangers areused for pulpy juices, ketchup, and oil refineries | Scraped surface exchangers are commonly used for Ketchup, Mayonnaise, Spreads and fillings, Sauces and puddings, Baby food |
Conclusion
The article was an attempt to deliver all the essential information about what Heat Exchanger is and which type of Heat Exchangers is suitable for your product. Not many documents are available that simplify heat exchanger and compares different aspects of a heat exchanger.
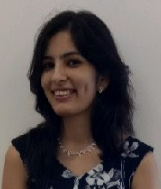